VIDEO & CENTER
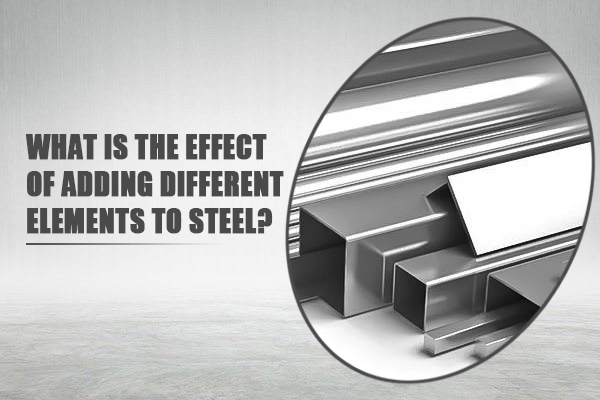
A certain amount of metal or non-metal elements are added in the smelting process to improve and increase the strength of steel, improve oxidation resistance, improve plasticity and process performance. The added elements are called alloying elements. Commonly used alloying elements are manganese Mn, silicon Si, chromium Cr, nickel Ni, molybdenum Mo, tungsten W, titanium Ti, cobalt Co, aluminum Al, boron B, copper Cu and so on.
chromium
Chromium can increase the hardenability of steel, can improve the strength and wear resistance of steel. It has good high temperature oxidation resistance and corrosion resistance. Chromium is the main alloying element of stainless acid-resistant steel and heat-resistant steel.
Chromium can improve the strength and hardness of carbon steel in rolling state, and reduce the elongation and shrinkage of section. When the chromium content exceeds 15%, the strength and hardness will decrease, and the elongation and section shrinkage will increase accordingly.
Spring steels containing chromium are not easy to decarburize during heat treatment. Chromium can improve the wear resistance, hardness and red hardness of tool steel, and has good tempering stability.
nickel
Nickel strengthens ferrite and refines pearlite in steel, the overall effect is to increase strength, and the effect on plasticity is not significant. Generally speaking, for low carbon steel used in rolled, normalized or annealed state without tempering treatment, a certain nickel content can improve the strength of the steel without significantly reducing its toughness. With the increase of nickel content, the yield of steel is faster than the tensile strength, so the nickel steel is higher than the ordinary carbon steel. While improving the strength of steel, nickel has less impact on the toughness, plasticity and other process properties of steel than other alloying elements. For medium carbon steel, the pearlite becomes thinner because nickel reduces the pearlite transition temperature. And because nickel reduces the carbon content of the eutectoid point, the pearlite quantity is more than that of carbon steel with the same carbon content, so that the strength of pearlite ferritic steel with nickel is higher than that of carbon steel with the same carbon content.
Therefore, nickel added to steel is not only acid resistant, but also alkali resistant, corrosion resistant to atmosphere and salt, nickel is one of the important elements in stainless acid-resistant steel.
molybdenum
Molybdenum in steel can improve hardenability and thermal strength, prevent temper brittleness, increase remanence and coercivity and corrosion resistance in some media.
In tempered steel, molybdenum can make the parts of large section quench deep, quench through, improve the tempering resistance or tempering stability of steel.
In carburized steel, molybdenum in addition to the above role, but also in the carburizing layer to reduce the carbide in the grain boundary to form a continuous network tendency, reduce the residual austenite in the carburizing layer, relatively increase the wear resistance of the surface layer.
tungsten
In addition to forming carbides in steel, tungsten is partially dissolved into iron to form a solid solution. The main use of tungsten in steel is to increase tempering stability, red hardness, thermal strength and increased wear resistance due to the formation of carbides. Therefore, it is mainly used in tool steel, such as high-speed steel, hot forging die steel and so on.
Tungsten forms refractory carbides in high-quality spring steel, which can delay the accumulation process of carbides and maintain high high temperature strength when tempered at higher temperatures. Tungsten can also reduce the overheating sensitivity of steel, increase hardenability and increase hardness.
vanadium
Vanadium exists mainly in the form of carbide in steel. The main function is to refine the structure and grain of steel, reduce the overheating sensitivity of steel, and improve the strength and toughness of steel.
In low alloy steel, vanadium can refine grain, improve the strength and yield ratio after normalizing and low temperature toughness, and improve the weldability of steel.
Vanadium in alloy structural steel due to the general heat treatment conditions will reduce the hardenability, so it is often used in combination with manganese, chromium, molybdenum and tungsten in structural steel.
In tempered steel, vanadium is mainly used to improve the strength and yield ratio of steel, refine the grain and reduce the sensitivity of overheating.
In spring steel and bearing steel, vanadium can improve the strength and yield ratio, especially increase the proportional limit and elastic limit, reduce the decarbonization sensitivity during heat treatment, and thus improve the surface quality.
titanium
Titanium is a good deoxidizing agent and an effective element for fixing nitrogen and carbon. Titanium carbide binding force is strong, stable, not easy to decompose, in steel only heated to more than 1000℃ to slowly dissolve into the solid solution. Since the affinity between titanium and carbon is much greater than that between chromium and carbon, titanium is commonly used in stainless steel to fix the carbon in it to eliminate the depletion of chromium at the grain boundary, thereby eliminating or reducing the intergranular corrosion of steel.
Titanium can improve plasticity and toughness in ordinary low alloy steel. The alloy structural steel containing titanium has good mechanical properties and process properties, and the main disadvantage is that the hardenability is slightly poor.
zirconium
Zirconium is a strong carbide forming element, and its role in steel is similar to niobium, titanium, vanadium. Adding a small amount of zirconium has the effect of degassing, purifying and refining grains, which is conducive to the low temperature performance of steel and improving the stamping performance. It is often used in the manufacture of ultra-high strength steel and nickel-based superalloy used in the structure of gas engines and ballistic missiles.
cobalt
Cobalt is mostly used in special steel alloys, high-speed steel containing cobalt has high temperature hardness, and molybdenum can be added to maraging steel at the same time to obtain ultra-high strength and good comprehensive mechanical properties.
Cobalt reduces the hardenability of steel, therefore, adding carbon steel alone will reduce the comprehensive mechanical properties after tempering. Cobalt can strengthen ferrite, added to carbon steel, annealed or normalized state can improve the hardness of steel, yield point and tensile strength, elongation and section shrinkage have adverse effects, impact toughness also decreases with the increase of cobalt content. Because of its oxidation resistance, cobalt is used in heat-resistant steels and heat-resistant alloys.
silicon
Silicon can be dissolved in ferrite and austenite to improve the hardness and strength of steel. When the silicon content exceeds 3%, the plasticity and toughness of the steel will be significantly reduced. Silicon can improve the elastic limit, yield strength and yield ratio, and fatigue strength and fatigue ratio of steel. This is the reason why silicon or silicon manganese steel can be used as spring steel.
manganous
Manganese is a good deoxidizer and desulfurizer. Steel generally contains a certain amount of manganese, which can eliminate or weaken the hot brittleness of steel caused by sulfur, thereby improving the hot working performance of steel.
Manganese has the characteristics of rich resources and diverse performance, and has been widely used, such as carbon structural steel with high manganese content and spring steel.
aluminium
Aluminum is mainly used for deoxidation and grain refinement. Aluminum can inhibit the aging of low carbon steel and improve the toughness of steel at low temperature. When the content is high, it can improve the corrosion resistance in the oxidation resistance of steel, and improve the electrical and magnetic properties of steel. Aluminum plays a great role in solid solution strengthening in steel, improving the wear resistance, fatigue strength and core mechanical properties of carburized steel.
In heat-resistant alloys, aluminum and nickel form compounds that increase thermal strength. The Fe-Cr aluminum alloy containing aluminum has the characteristics of near constant resistance and excellent oxidation resistance at high temperature, and is suitable for electric heating alloy materials, such as chrome-al resistance wire.
copper
The protruding effect of copper in steel is to improve the atmospheric corrosion resistance of ordinary low alloy steel, especially when used with phosphorus, the addition of copper can also improve the strength and yield ratio of steel, and has no adverse effect on the welding performance.
boron
The main role of boron in steel is to increase the hardenability of steel, thereby saving other rarer and more expensive metals, such as nickel, chromium, molybdenum and so on. It can replace 1.6% nickel, 0.3% chromium or 0.2% molybdenum, with boron to replace molybdenum should be noted, because molybdenum can prevent or reduce the tempering brittleness, while boron slightly promote the tempering brittleness tendency, so can not use boron to replace molybdenum completely.
Spring steel is generally required to be fully quenched, usually the spring section is not large, and the use of boron-containing steel is advantageous. The action of boron on high silicon spring steel fluctuates greatly, so it is inconvenient to use.
Boron has a strong affinity with nitrogen and oxygen, adding 0.007% boron to the boiling steel can eliminate the aging phenomenon of steel.
Rare earth Re
Generally referred to as rare earth elements, refers to the periodic table of elements atomic number 57~71 lanthanide elements, plus 21 scandium and 39 yttrium, a total of 17 elements.
Rare earth elements can improve the plasticity and impact toughness of forged rolled steel, especially in cast steel. It can also improve the creep resistance of heat-resistant steels, electric heating alloys and superalloys.
Rare earth elements can also improve the oxidation resistance and corrosion resistance of steel.
nitrogen
Nitrogen can be partially dissolved in iron, and has the effect of solid solution strengthening and improving hardenability, but it is not significant. Due to the precipitation of nitride on the grain boundary, the high temperature strength of the grain boundary can be increased and the creep strength of the steel can be increased. Combined with other elements in steel, precipitation hardening effect. After nitriding the surface of the steel, it not only increases its hardness and wear resistance, but also significantly improves the corrosion resistance. In mild carbon steel, residual nitrogen can cause aging brittleness.
sulfur
Sulfur is seriously segregated in steel, deteriorates the quality of steel, reduces the plasticity of steel at high temperatures, and is a harmful element. In order to prevent brittleness caused by thinning, enough manganese should be added to form MnS with a higher melting point.
phosphorus
Phosphorus has strong effect on solid solution strengthening and cold hardening in steel. The addition of low alloy structural steel as alloying element can improve its strength and atmospheric corrosion resistance, but reduce its cold stamping performance.
The combined use of phosphorus with sulfur and manganese can increase the cutting performance of steel and increase the surface quality of the workpiece, which is used for easy cutting steel, so the phosphorus content of easy cutting steel is also high.
Phosphorus soluble in ferrite, although it can improve the strength and hardness of steel, the biggest harm is serious segregation, increase tempering brittleness, significantly reduce the plasticity and toughness of steel, resulting in steel in cold processing is easy to crack, that is, the so-called "cold brittleness" phenomenon.
Phosphorus is a harmful element, should be strictly controlled, the general content is not more than 0.030%~0.040%.