VIDEO & CENTER
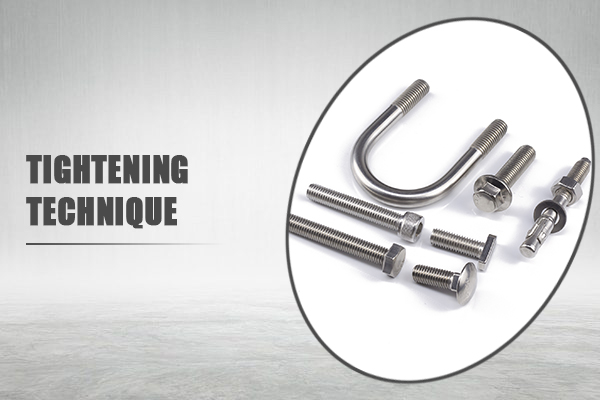
Tightening is to apply appropriate clamping force at the joint so that the connector can work normally and play its function. Understanding tightening technology is important to select a tightening solution that meets your specific needs
About threaded connection
Threaded connections are a common part connection because of their simple design, ease of assembly and disassembly, and many advantages in terms of production efficiency and ultimately cost. Threads are subjected to tensile loads, torsional loads, and sometimes shear loads. The tensile load corresponds to the clamping force of the connector. Because it is difficult to measure the clamping force directly, tightening torque is usually used to control when the tensile load of the bolt and the clamping force are relative to each other.
Tightening process
The tightening process has an important effect on the quality of the threaded connection. The goal of the tightening process is to apply enough clamping force to hold the connectors together. The smaller the dispersion of clamping force in tightening process, the better the connection effect. The tightening process depends on: • how torque is applied; Manual tightening, direct drive or non-direct drive. • Tightening control: torque, Angle or gradient. • Monitoring: A tool or system that monitors both controlled and uncontrolled parameters • gives operators greater confidence in connection processes and quality.
Different ways of applying torque
Manual tightening is often done using a torque wrench. The wrench is set to a preset torque value and the operator is alerted when the correct torque is reached. The advantage of this solution is that it is easy to set up and use. The disadvantage is that the production efficiency is low, the tightening control function is limited, and even the use of advanced types of wrenches (measurable control Angle) also has the problem of low productivity. Direct drive tools can be electrically or pneumatic powered. In general, air tools will stop running through a mechanical clutch when a set torque is reached, while power tools can be equipped with sensors to monitor torque, Angle and gradient. Monitoring more process parameters can improve the confidence of the tightening process. The non-direct drive method uses the principle of inertia to release the driving force intermittently during tightening, which is the way impact tools and pulse tools work. The advantages of this series of tools are high torque, low reaction force and fast tightening. The disadvantage is that the clamping force is usually more dispersed than with direct drive tools. Such tools are usually not equipped with any sensors, but sometimes there are tools equipped with sensors. In general, direct-drive tools have a lower dispersion of clamping force when using gradient control and Angle control than the torque control of shock/pulse tools. If more advanced monitoring and control methods are used, the size of the fastener can be reduced, thereby reducing the weight of the product. However, this must be determined at the product design stage what type of tools to use.