VIDEO & CENTER
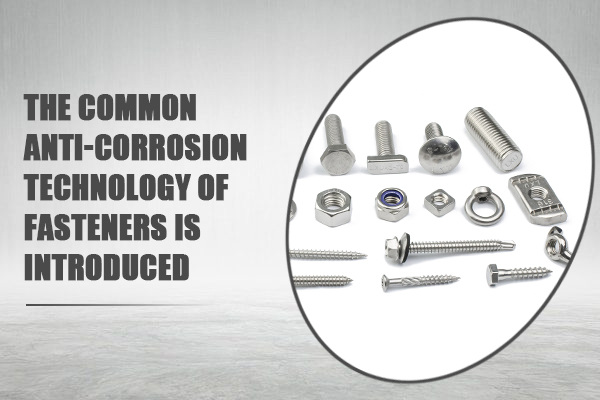
Fasteners are the most common parts of mechanical equipment used for fastening connections, which are used in a specific environment, and the long-term interaction between fasteners and the environment will always change their status and performance, that is, corrosion, which is one of the main forms of fastener failure." Fastener corrosion light will affect the thread can be disassembled and repeated installation, heavy will damage the strength of the connection between the parts, and even lead to the sudden failure of the workpiece, resulting in catastrophic accidents, so the corrosion of fasteners has been a topic of great concern.
Common anti-corrosion technology of fasteners
The anti-corrosion treatment of fasteners is generally through a certain method to form a covering layer or anti-corrosion layer on the surface of the workpiece to hinder the influence of the external environment on the fastener itself, to achieve the effect of corrosion resistance. There are mainly four kinds of anti-corrosion technology for fasteners: film treatment technology, metal coating technology, coating technology and changing the internal structure of the metal (such as stainless steel).
- Membrane treatment technology
Film treatment technology mainly refers to the treatment process of using chemical or electrochemical methods to generate a stable chemical (electrochemical) conversion film on the surface of the metal. For example, in urban rail vehicles, the film treatment of fasteners is more black/blue treatment and phosphating treatment.
1.1. Black and blue
In a concentrated alkaline solution containing oxidants, the process of forming a layer of chemical oxidation film on the surface of steel parts (the main component is Fe,O,) after being treated at about 140C for a certain time.
Technical features of blackening/bluing:
1) Film thickness 0.5-1.5μm.
2) The neutral salt spray test (NSS) is generally only 2 to 5 Hrs, at which time the oxide film has broken, and even a lot of rust will appear, as shown in Figure 1.
3) Low hydrogen embrittlement sensitivity, can be used as high strength bolts.
4) As a fastener, its torque and preload consistency is poor.
5) The color is brighter and the decorative effect is better.
6) Low cost.
1.2. Phosphating treatment
The process by which steel parts are immersed in a solution containing manganese, phosphoric acid, phosphate and other reagents to generate a phosphate conversion film that is insoluble in water on the metal surface is called phosphating. Technical characteristics of phosphating treatment.
1) The film layer is firmly bound to the matrix (1 ~50 μm thick).
2)NSS up to 10~20 Hrs or even 72 Hrs.
3) Poor mechanical strength, brittle quality.
4) As a fastener, its torque-preload consistency is very good.
5) The color is light gray and other dark color, the decorative effect is poor.
6) Hydrogen embrittlement sensitivity is low, can be used as high strength bolts.
7) Lower cost.
2, metal coating technology
Metal coating technology is mainly used on the surface of metal materials to form a thin layer of metal, in order to give metal materials decorative or protective surface treatment process. In urban rail vehicles, the metal coating technology of fasteners is mainly galvanized, and other special metal coatings (chrome plating, nickel plating, cadmium plating, silver plating, etc.).
2.1 Galvanizing
Zinc and iron can be miscible, its standard electrode potential is -0.76V, for the steel substrate, zinc coating belongs to the anodic coating, can better protect the steel substrate, so galvanized technology is widely used in fasteners. There are three commonly used galvanizing methods: hot dip galvanizing, electric galvanizing and mechanical galvanizing.
2.1.1 Hot dip galvanizing
Hot dip galvanizing means that steel parts are immersed in molten liquid zinc, so that a series of physical and chemical reactions occur on the surface of the workpiece, thereby forming a metal galvanizing layer. Hot dip galvanized coating thickness is very thick (up to 30 ~ 60μm), its corrosion resistance is very good, widely used in outdoor long-term use of steel parts (such as TV tower, highway guardrail, etc.). For fasteners, hot-dip galvanizing is generally suitable for M6 and above bolts, but it cannot be used for high-strength fasteners, mainly because the operating temperature of the hot-dip galvanizing process is very high (400C~500C), which is easy to temper and soften high-strength fasteners.
2.1.2 Galvanizing
Electrogalvanizing is the use of electrolysis to form a uniform, dense and well-combined galvanizing layer on the surface of steel parts. The thickness of the zinc layer of galvanizing is thin (5~30μm), and the corrosion resistance is the worst in the galvanizing anti-corrosion treatment, but its process is simple, the cost is low, and the impact on the threading problem is also small, and it is widely used in fasteners. Because electrogalvanizing has a high hydrogen embrittance sensitivity, and it is difficult to completely complete the dehydrogenation (the surface of the electrogalvanizing layer will peel or fall off above 100C), so electrogalvanizing can not be used for high-strength fasteners.
2.1.3 Mechanical galvanizing
Mechanical galvanizing refers to the surface treatment process of forming galvanized layer by using impact medium to impact the surface of steel parts under the action of zinc powder, dispersant and accelerator. The thickness of mechanical galvanized layer is generally 5 ~ 50μm, the coating surface is compact and uniform, the decorative effect is good, and the corrosion resistance is excellent. And the coating without high temperature tempering, no hydrogen embrittlement and other hot dip galvanizing, electrogalvanizing shortcomings, is a particularly suitable for fastener anticorrosion surface treatment process.
2.2. Other metal coatings
2.2.1 Chrome plating
As a metal coating, chromium has strong adhesion, good wear resistance, excellent decorative effect, and high heat resistance (below 500C can be used normally), so the chromium coating as a metal coating of fasteners is very ideal.
Chrome plating treatment mainly has the following disadvantages:
1) The process is complex, and nickel or copper must be plated before chromium plating.
2) Expensive.
3) Chromium coating is hard, brittle and easy to fall off.
2.2.2 Nickel plating
Nickel as a metal coating has good electrical conductivity, high hardness, good decorative effect, good heat resistance (below 600C can be used normally), so the fastener using nickel plating treatment is also more ideal.
Nickel plating treatment mainly has the following disadvantages:
1) The process is complex, and copper must be plated before chrome plating.
2) The nickel coating is porous, and the thin coating will accelerate the corrosion of the matrix.
3) Expensive.
2.2.3 Cadmium plating
As a metal coating, cadmium is an anodized coating, which has strong hydrochloric acid corrosion resistance, low hydrogen brittleness, and good decorative effect. It is especially suitable for fasteners in Marine environment applications (such as fasteners for Hainan airlines aircraft and oil drilling platforms).
Cadmium plating treatment mainly has the following disadvantages:
① High environmental pollution, cadmium melting gas and soluble cadmium salt are toxic.
② Expensive.
2.2.4 Silver plating
Silver as a metal coating has excellent electrical conductivity, excellent reflective performance, good lubricity and excellent heat resistance (below 870C can be used normally), so silver plating treatment is widely used in electronic and electrical, high-frequency components and other fields (such as generator conductive bolts, vehicle battery terminals).
Silver plating treatment mainly has the following disadvantages:
① The process is complex, and copper must be plated before silver plating.
② The price is very expensive.
2.2.5 Galvanized nickel
Zinc-ni composite coating is a new type of alloy metal coating optimized on the surface treatment of zinc-plating, which has many advantages.
1)NSS can reach 500-1500Hrs.
2) The electrode potential of the coating is between Fe and Zn, which is more suitable for aluminum assembly.
3) The coating hardness is high, the decorative effect is very good.
4) Almost no hydrogen embrittlement, can be used for high strength fasteners.
5) Good heat resistance (below 8009C can be used normally).
The main disadvantage of zinc nickel coating: it is a higher price (about 6 times that of galvanized), but its excellent comprehensive performance has been more and more widely recognized by people.
- Coating technology
Coating technology refers to the specific paint with a certain equipment and way coated on the surface of the object, so that the surface of the dense, continuous, uniform film, and then by natural or. A surface treatment technique for drying and curing to form a protective or decorative coating.
In fasteners, the most widely used coating technology is zinc-chromium coating technology, which is a coating that is coated with zinc-chromium coating on steel parts and formed on the surface of steel parts through full closed cycle coating and baking, also known as Dacromet treatment, which has the following excellent characteristics.
1)NSS up to 500 ~ 1000 Hrs.
2) Good permeability.
3) No hydrogen embrittlement sensitivity.
4) Low environmental pollution.
5) As a fastener, its torque-preload consistency is very good.
6) The price is moderate (about 2 times of galvanized).
Dacromet processing mainly has the following disadvantages:
1) Poor wear resistance (hardness is only 1 H).
2) The color is single (only silver white and silver gray), and the decorative effect is poor.
3) Poor electrical conductivity, not suitable for electrically connected parts.
- Change the organizational form of steel
4.1 Composition changes (such as stainless steel)
Stainless steel is the abbreviation of stainless steel, which has excellent corrosion resistance and good decorative effect, and has a wide range of applications in various cities. It is generally believed that the corrosion resistance mechanism of stainless steel is mainly as follows.
1) When Cr content exceeds 13%, the electrode potential of steel will rise from negative electrode potential to positive electrode potential, so that the steel matrix itself is "inert";
2)Cr will form a dense Cr-rich passivation film on the surface of the steel, thereby further protecting the matrix.
3) Stainless steel is divided into: martensitic steel, ferritic steel, austenitic steel, austenitic ferritic stainless steel, etc., especially austenitic stainless steel has the best corrosion resistance, such as A2, A4 stainless steel.
Stainless steel mainly has the following shortcomings :① the yield strength is very low (generally not more than 300 MPa), not suitable for the connection of major structural parts.
② Easy to appear thread bite. When the stainless steel bolt is tightened, it is easy to cause damage to the surface of the thread, and at this time, it will spontaneously produce an oxide layer, which will aggravate the bolt sticking and locking.
③ Easy to produce intergranular corrosion. At a certain temperature, C and Cr in stainless steel will form compounds, especially near the grain boundaries, which will cause a "poor Cr zone" in the grain boundaries, resulting in grain boundary corrosion.
④ Poor corrosion resistance to CI media (except A4 stainless steel).
⑤ The price is higher (about 4 times that of dacromet).
4.2 Change of heat treatment state
Steel materials are mainly polyphase structures (impurities, carbides, intermetallic compounds and other second phases are usually present in steel as cathodes, and Fe matrix as anodes). There is a potential difference between phases in the polyphase structure, which results in corrosion microcells. The second phase may be the anode passivation phase or the cathode dissolution phase, both of which will affect the corrosion resistance of the matrix.
For example, stainless steel, which should be very careful when welding and heat treatment. Stainless steel after high temperature solution treatment, heating between 400C~850C, a large number of CrsC. And C; Carbides precipitate along the grain boundary, resulting in the formation of Cr poor zone near the grain boundary. Carbide is used as the cathode of the corrosion battery, and the poor Cr region is used as the anode of the corrosion battery, which leads to grain boundary corrosion, and its corrosion resistance will be greatly reduced.