VIDEO & CENTER
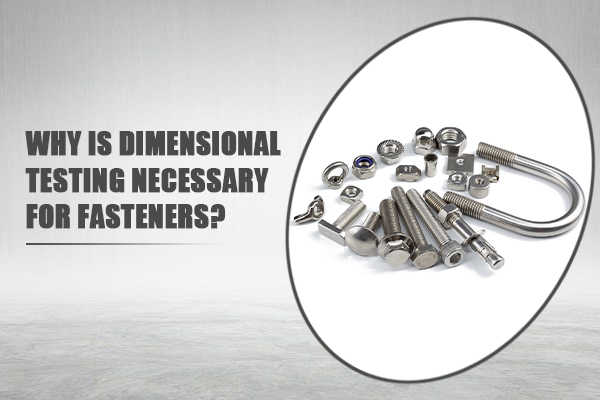
The measurement of fastener size is the key link of quality control, which is directly related to whether the fastener can meet the design requirements and use functions.
By measuring the diameter, length, thread specifications and other parameters of the fastener, it can be judged whether it meets the design requirements, so as to prevent the connection loosening or failure caused by the size mismatch. This detection not only ensures the safety of the connection, reduces the risk of accidents and accidents, but also ensures the reliability of the connection, can withstand the load and pressure under the design requirements, and meet the needs of long-term use.
In addition, the fastener size detection plays an important role in the manufacturing process, which ensures that the size, shape, material and performance of the fastener meet the requirements, thus ensuring the quality and performance of the product.
This is critical for many sectors, including the automotive industry, aerospace industry, building and structural engineering, and electronic and electrical equipment. For example, in the automotive manufacturing process, fasteners for key components such as the engine, chassis and brake system are subjected to rigorous dimensional testing to ensure safety and reliability.
Similarly, in aerospace equipment, the size and quality of fasteners are critical to flight safety. In construction and structural projects, the dimensional inspection of fasteners ensures the stability and bearing capacity of the connection and guarantees the safe operation of the project.
In the manufacture of electronic and electrical equipment, fasteners are dimensioned to ensure the secure connection of equipment and prevent failure and damage.